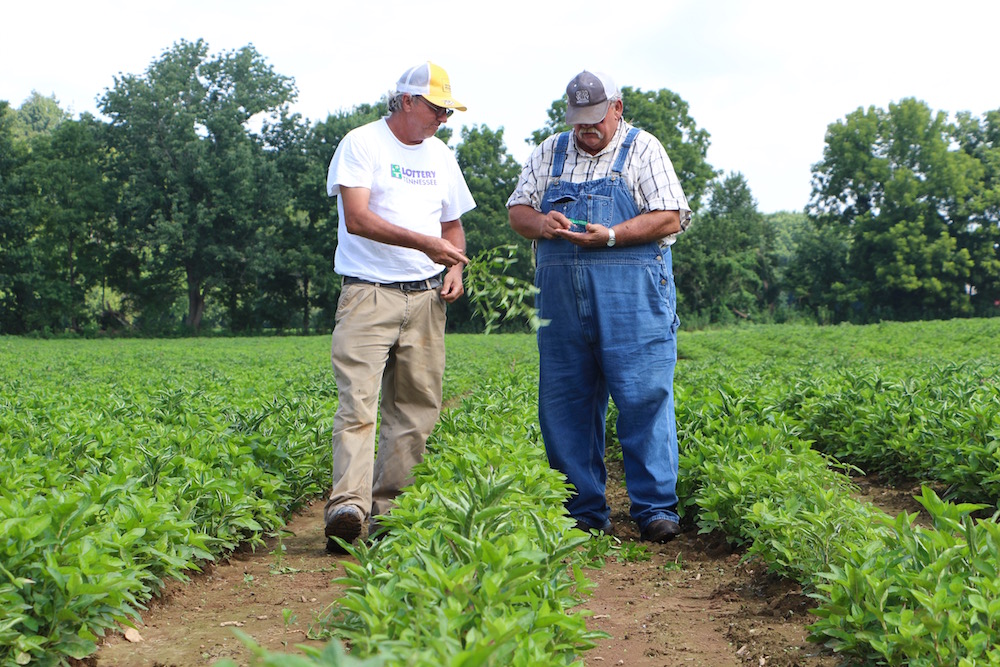
Tobacco is still the biggest cash crop in many Tennessee fields, as it’s been for generations.
But farmers are looking for other options that aren’t quite so difficult to grow. And some, like David Fulton in Robertson County, are turning to an unusual crop: indigo — the plant that can be used to dye denim.
Fulton unlocks a gate on the side of a quiet backcountry road. Behind it is a small field bordered by trees. It’s just 4 acres, out of a thousand that he farms.
“OK,” he says. “Let’s go look at some indigo.”
Startup Crop
The first thing to know about indigo plants is that they are, in fact, green. They look like tiny bushes growing in neat rows.
“Evidently, it appears to be doing something right,” Fulton says, eyeing the field. “I don’t really know what it’s supposed to look like, but that right there looks pretty good to me.”
There’s a lot he doesn’t know about indigo yet, including some basic things, like: How do these green plants turn into blue dye?
This is his first year growing indigo, and his
neighbor, Larry Williams, is also growing it for the first time. He points to one of Fulton’s plants.
“I saw a leaf right there somewhere that has some purple in it, some color in it,” Williams says.
“The dye is actually going to come at the bloom,” Fulton says, pointing to where the plants will flower.
“I thought it was the leaf itself,”
Williams says.
It turns out, Williams is right. The dye does come from the leaf.
It’s not that these men didn’t do their research. They tried to, Fulton says. There’s just not much information out there about growing indigo. The last time the crop was commercially grown in this part of the world was before the American Revolution — 240 years ago.
A Hard Lifeline
When it comes to tobacco, though, these men are experts.
Despite all the changes in the industry over the past few decades, tobacco is still big business in Robertson County, just north of Nashville. Production has barely dipped since the early ’90s, according to Paul Hart, University of Tennessee’s extension agent in Robertson County.
Fulton and Williams are both in their
50s,
and they’ve worked in tobacco fields since they were kids.
It’s paid for mortgages. It’s sent children to college.
Williams says it’s also just part of who they are.
“I’m the fifth generation on my farm,” he says. “Grandfathers, great-grandfathers, raised tobacco.”
It’s easy to get nostalgic about tobacco this time of year, during the harvest. Fulton points out barns where, soon, they’ll cure the leaves they’ve harvested, smoking them with smoldering wood for weeks.
“People will stop and say, ‘My god, your barn’s on fire!’ And I say, ‘No, that’s just part of it,’ ” he says.
“You’ll know the smell when you go by the barn,” Williams adds. “It’s a feeling of, the harvest is over. It’s just a good feeling.
“
But the rest of the year, raising tobacco is not particularly fun or easy. It’s a finicky crop, susceptible to diseases, and it’s extremely labor-intensive. Every part of the process is done by hand — from the planting to the harvesting and curing — and this next generation isn’t sticking around to do it.
“The labor doesn’t seem to be out there anymore. None of the young people want to work in tobacco. It’s a nasty job. Every bit of it is hot and nasty,” Williams says.
“Can’t blame ’em.”
Easier Alternatives
Labor has gotten more expensive, which cuts into profits. So even though tobacco is what they know, both men have been on the lookout for alternatives — things that are easier to grow and can still make some money.
Then, earlier this year, they heard about a local company called Stony Creek Colors. The startup had developed a method of planting indigo that uses the same equipment as tobacco, Williams says,
“so we didn’t have to go out and purchase anything special.”
Stony Creek also created a machine to harvest the crop, and people from the company will come out to the farm and do it themselves. Literally, all these farmers have to do is make sure the indigo stays alive through the season.
The downside: They won’t make as much money as they would selling tobacco. But it’s so much easier, says
Sarah
Bellos
, the founder of Stony Creek.
“We’re not trying to compete on per-acre price basis with tobacco. We are trying to make the margins for the farmer good for growing indigo,” she says.
Her company is four years old and still very much in the startup phase, just trying to prove to investors that the business model works. The natural indigo market barely exists anywhere in the world these days. For the last century, almost all indigo dye has been made synthetically with no farming involved.
But Bellos wants to bring it back. She’s convinced that makers and consumers of high-end jeans will pay more for natural indigo — and at some point, she says, maybe the mass market would too.
“So if farmers can grow them, and we can bring chemical manufacturing jobs back to the U.S., that’s something that’s worth investing in.”
And so far, the company is making it work. A denim manufacturer in North Carolina is buying all of its indigo crop this year. In Tennessee,
Stony Creek is still a small operation, with only 10 farmers growing 30 acres of indigo. But Fulton says he knows more people who are already interested.
“I bet I’ve had 50 farmers call,” he says. “It’s been very interesting, no doubt about that.”
So, will indigo replace tobacco? Fulton says, not any time soon. It’s just not lucrative enough.
But he wants the crop to succeed — partly because it would be good for his farm, and partly because it would help his community. Stony Creek will process the indigo dye in a renovated plant down the road, which is creating 50 jobs.
It’s fitting that the renovated plant used to process tobacco.
This story has been updated to correct the name of Larry Williams.
